Lyophilization, also known as freeze-drying, plays an essential role in the pharmaceutical industry. This industry has been using freeze-drying techniques for many years to extend the shelf life of various medicines.
How exactly does lyophilization work? What does a lyophilizer do, and why is this cryogenic application so valuable for the pharmaceutical industry? Read on for detailed answers to these questions.
What is lyophilization?
Lyophilization takes place in a freeze dryer. In this (often) cryogenic freezer, a product is first brought to a low temperature, after which almost all the moisture is removed from it.
In most cases, this process consists of three steps:
1. Freezing the product.
Lyophilization begins with freezing a product at a temperature of around -40°C to -50°C at atmospheric pressure. Liquid nitrogen is often used during this phase as a fast, environmentally friendly, and affordable refrigerant. Rapid freezing can be essential when freeze-drying substances that are sensitive to crystal formation.
The product is cooled to below the triple point during this first stage. This ensures that sublimation, rather than melting, occurs in the primary drying phase.
Source: Na Eye
The triple point of water
2. Primary drying phase (sublimation).
Next, the cooled product is slightly heated at a reduced pressure, which causes the sublimation, as mentioned earlier, to take place. A vacuum is also created in the freeze dryer, further accelerating the sublimation process.
During this phase, the formed water vapors are accumulated by a condenser, which causes the vapors to take on a solid form.
The vast majority of moisture is removed from the product during the primary drying phase, while its structure remains optimally intact.
3. Secondary drying phase (absorption)
In the final stage, secondary drying, known as absorption, takes place. The ionically bonded water molecules are extracted from the product during this phase.
During this phase, the temperature rises slightly, sometimes even above 0 °C. The vacuum is then breached using an inert gas, such as nitrogen, after which the product is sealed.
On completing these three steps, the product has a porous shape and often contains no more than 1-4% water.
Lyophilization in the pharmaceutical industry
Lyophilization is mainly used in the food industry for food preservation and in the pharmaceutical industry to produce and preserve (mainly biopharmaceutical) pharmaceuticals.
Many of these pharmaceuticals contain complex molecular structures, which are unstable in liquid form. Therefore, if these medicines are stored undried, their shelf life is limited.
When the moisture is removed from the structures, they stabilize considerably, allowing the medication to be stored for an extended period and reconstituted later by adding moisture again.
Examples of pharmaceutical materials treated using lyophilization are antibiotics, vaccines, bacteria, and diagnostic drugs.
The above diagram of Lubrizol CDMO clearly shows the process of lyophilization in the pharmaceutical industry. The vials containing the drug are cooled and dried by using a condenser. A vacuum is also created in the application to speed up the sublimation process.
Challenges with lyophilization
Lyophilization is a complex process involving several challenges. For example, the composition of each substance or drug is different, and how to perform the lyophilization must be examined for each material. All aspects and components of the process must be perfectly matched to the specific material to avoid damage. This research requires a lot of time and expertise.
During lyophilization, products are exposed to the environment for a considerable time, creating contamination risk. Sterile lyophilization is therefore extremely important, and freeze-dryers for drugs are subject to stringent safety requirements. Large-scale use of lyophilization is therefore costly.
Lyophilization and cryogenics
So, what is the role of cryogenics in lyophilization?
Freeze dryers can be found in many different forms. Small, large, and with different cooling systems. Mechanical or cryogenic. In the pharmaceutical industry, many freeze-dryers use liquid nitrogen for the first stage of the freeze-drying process: freezing the product.
Cryogenic freeze dryers offer several advantages, including:
- Low temperatures are easier achieved than with mechanical refrigeration. This is because liquid nitrogen has a temperature as low as – 196 °C.
- Cooling of the products is accomplished quicker, often a prerequisite for the lyophilization of vaccines.
- The system does not require refrigerants that are harmful to the environment.
- Compared to mechanical systems, the cost of cooling using liquid nitrogen is often lower.
- A cryogenic cooling system requires less maintenance, again reducing the overall cost of the system.
- A cryogenic cooling system is usually quieter than a mechanical system.
For these reasons, cryogenic lyophilization systems are prevalent in the pharmaceutical industry. Hence Demaco often works together with this industry and supplies the necessary infrastructures to make cryogenic lyophilization possible.
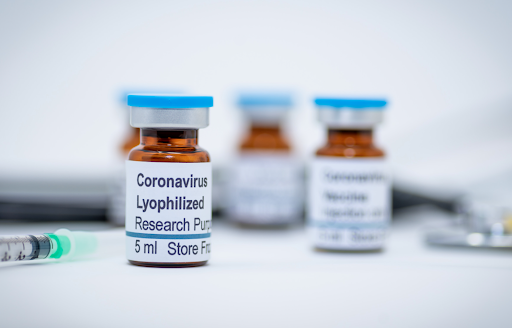
Demaco’s infrastructures for the pharmaceutical industry
For a cryogenic freeze dryer to function, cryogenic liquid is required. Which, in most cases, as outlined above, is liquid nitrogen.
Companies in the pharmaceutical industry that utilize cryogenic lyophilization have one or more cryogenic tanks, also known as dewars, located inside or outside their building. These dewars contain the required liquid nitrogen.
As an expert in cryogenic infrastructures, Demaco ensures that the liquid nitrogen reaches the freeze dryer at the proper pressure from these storage tanks while in optimum quality.
In cooperation with the customer, our experts evaluate the requirements for a specific cryogenic application. We will also provide the proper vacuum insulated transfer lines (VIP), the proper couplings, and any additional quality improvement products.
With years of experience in the pharmaceutical industry, we know exactly what a perfect infrastructure for a cryogenic freeze dryer needs.
Would you like to know more?
Do you have questions about the installation of a freeze dryer? Or would you like to know more about Demaco’s products and services? Feel free to contact us or take a look at our products and projects.